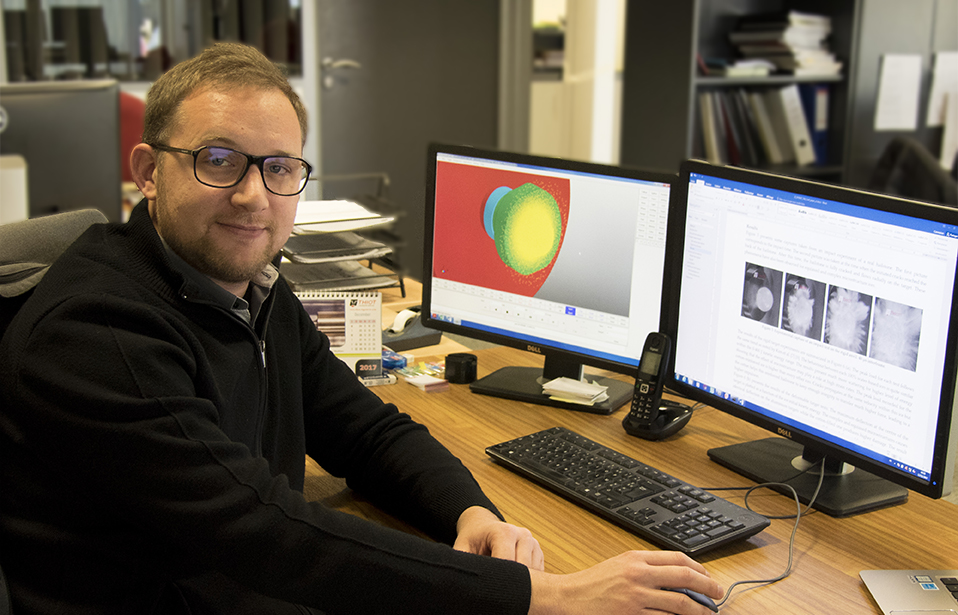
THIOT INGENIERIE is a partner in the RAPID IMPAGREL program, which aims to study and develop ice made to represent real hailstones in tests on aeronautical structures. Paul Deconinck, one of our doctors in shock physics, tells us more…
Paul, can you explain the context behind IMPAGREL?
It is part of the SME dual innovation support scheme RAPID. With RAPID, the French Defence Procurement Agency, DGA, wishes to facilitate the transfer of technology from universities to SMEs. One of the conditions is that the topics of study must be applicable to both the civilian and military spheres. This is indeed the case with IMPAGREL, which addresses the vulnerability of civil and military aeronautical structures against hailstone impacts. We have just entered the last year of this four-year programme.
What is the objective?
At the moment, aeronautical hailstone impact testing is regulated by standard ASTM-F320, which defines a protocol for producing the ice used in these tests. We know that a real hailstone is more resistant than ice produced in a freezer. Standard ASTM-F320 therefore proposes reinforcing the ice by adding cotton. However, the standard allows for substantial tolerance as to the quantity of cotton used, and the behaviour of the ice may therefore vary greatly according to the cotton content. With IMPAGREL, the aim is to eliminate the need to add cotton by developing ice with behaviour upon impact that resembles that of a real hailstone as closely as possible.
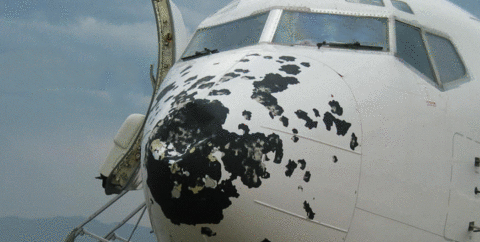
Who are the various partners involved in the project, and what are their respective roles?
Our partners are IGE (Institute for Geosciences and Environmental Research) in Grenoble, whose mission is to design and produce the ice, and LaMCoS (Contacts and Structure Mechanics Laboratory) in Lyon, which is dedicated to studying the quasi-static behaviour of the ice and the development of an appropriate behaviour model. THIOT INGENIERIE is responsible for studying the dynamic behaviour of the ice.
Why did your company wish to participate in this collaborative programme?
As a company offering impact testing services in our laboratory, in particular for the certification of aeronautical structures, the reason for getting involved was twofold. We will be able to carry out impact tests for our customers using ice that is as representative of real hail as possible, while benefiting from a reliable tailored behaviour model.
What steps does the programme involve?
The study started with the organisation of a hailstone collection in September 2015, in which approximately 30 hailstones measuring between 30 mm and 50 mm in diameter were recovered. This took place during a hailstorm in southwestern France.
IGE then analysed the microstructure of these hailstones, and LaMCoS studied their quasi-static behaviour. One of the important aspects of the mechanical behaviour of the hailstones lies in their complex microstructures. A detailed study of these microstructures enabled us to determine the size and shapes of the ice particles, as well as their crystallographic orientations. These analyses have been key elements governing the entire programme.
Could you go into more detail concerning the tests carried out by THIOT INGENIERIE?
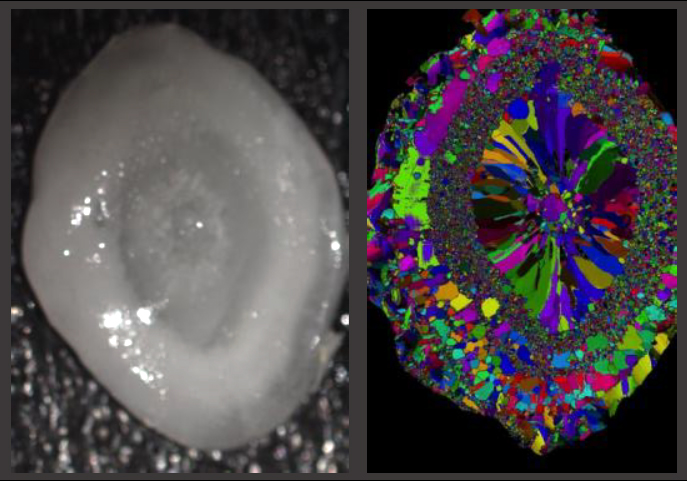
Above left: a cross-section of a hailstone. The modelling on the right shows the complexity of the different microstructures from which it is made.
Our company was responsible for studying the behaviour of the ice upon impact. The tests were conducted in our shock physics laboratory, using several speed ranges: up to 300 m/s for civil applications and between 800 and 1000 m/s for military applications. All the types of ice developed by IGE were characterised using various test configurations, as were a few hailstones that we shaped using an innovative process so that they corresponded to the geometries tested with the other types of ice.
Several types of test were performed, all using an array of instruments to recover as much data as possible. The first tests involved firing the ice onto a rigid structure while measuring the load transmitted and visualising the failure mechanisms using our high-speed camera. This type of test was conducted in order to study the behaviour of the ice itself. We also performed tests on deformable plates. This time, the purpose was to assess the ability of the ice to damage aeronautical structures. Finally, plate impact tests were carried out, allowing us to study the behaviour of the ice when subjected to shock stress as well as the phase changes and their effects during an impact. Modelling was of course the core concern throughout the study, being improved and enriched as the tests progressed.
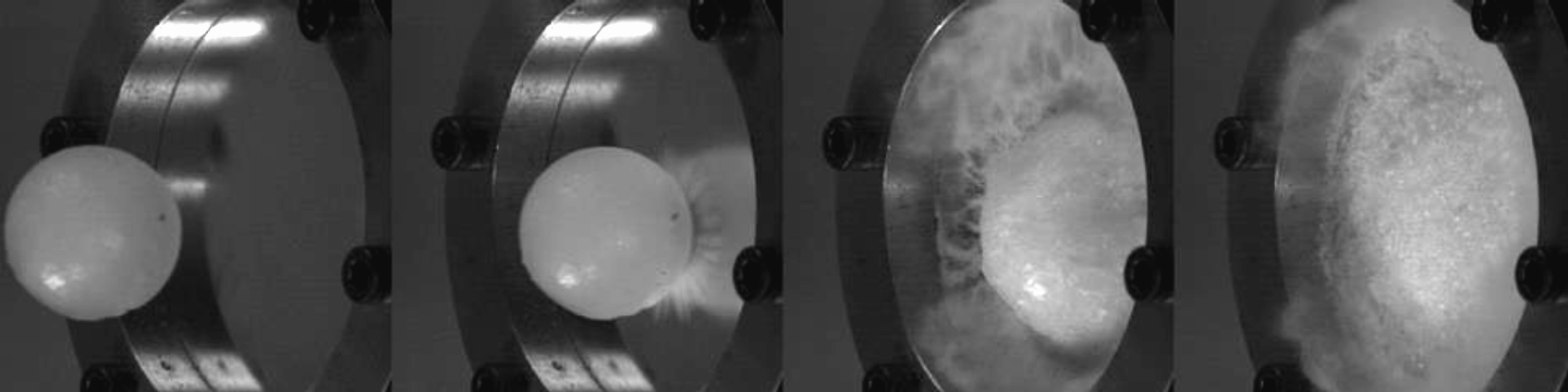
Above: impact of a hailstone (diameter: 40 mm) at 720 km/h.
Did the results meet your expectations?
Absolutely. This scientific approach has made us experts in the dynamic behaviour of ice. We are now able to offer our customers impact tests using ice representative of a real hailstone, and are able to control, for example, any problems related to withstanding acceleration in our launchers. The digital model that we have developed will allow us to efficiently identify the most appropriate test conditions and thus reduce the number of tests required. For our customers, this means even more reliable impact-test results and significantly shorter development phases.